What we offer ...
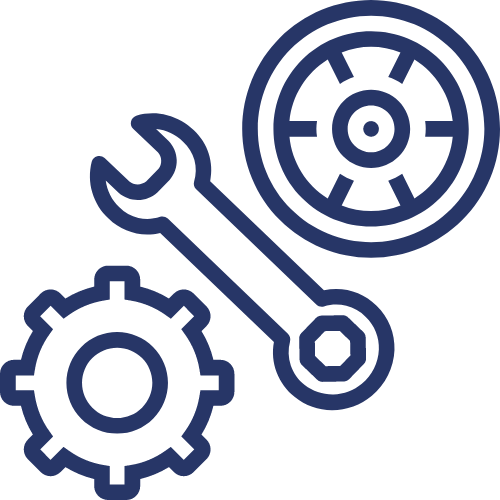
Assembly
We offer everything from simple assemblies to complete devices. Injection molded parts and supply cables from our own production, as well as required purchased parts can be assembled into complete, ready-to-use devices for you.
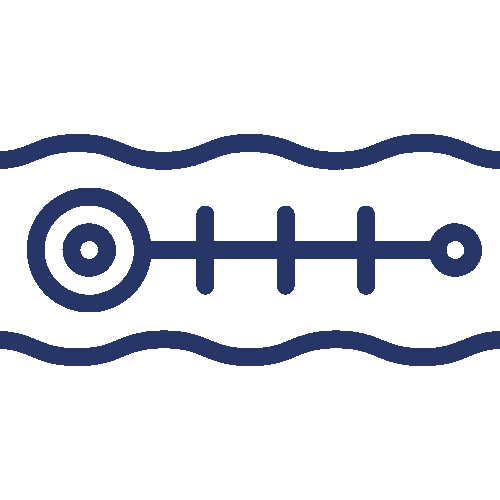
Further processing by joining
Ultrasonic welding, hot plate welding / mirror welding, hot gas welding, laser welding in toolmaking, bonding, screw connections, brass inserts for hot insertion and riveting.
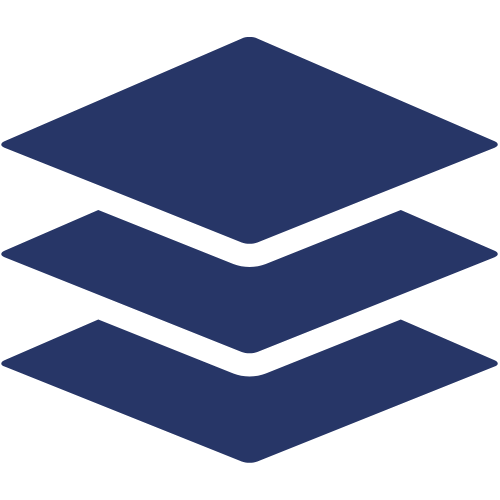
Coating by printing process
Pad printing process (single or two-component process with multiple colors) and hot stamping
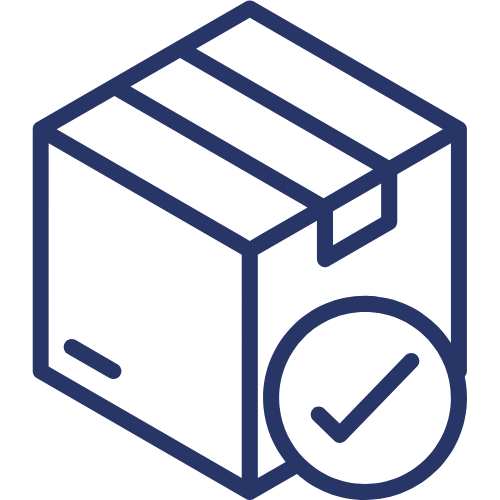
Packing
On request, your ordered goods can be dispatched directly in your individual sales packaging. Otherwise, we will deliver your order in our own packaging.
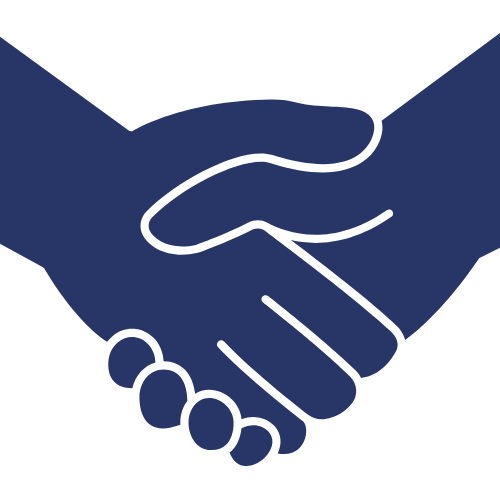
External partners
In cooperation with external partners, we offer the coating steps vapor deposition, electroplating and painting with further processing at our company.
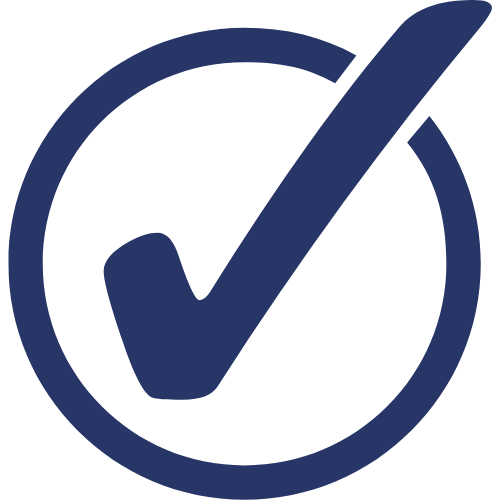
Safety checks
We carry out all the necessary safety checks in the company to ensure that the safety standards are met and that you receive a high-quality product.